Working on a new board. Design completed. Printing has begun. WooHoo! I am planning to glass this by wetting out the glass on a table then transferring to the board. I’ll be using a Sun Cure/ Solarez resin this time around so that I can work slowly and hopefully get a better finish. Stay tuned for updates and another project log.
Author Archives: TheBogueRat
3d Printed Surfboard
I’ve been working a long time on this. Go check out the full details on this page.
First Homebrew PCB
I finally etched my first board! I bought my first 2 layer copper clad and some peel-n-stick traces more than 20 years ago. They’ve been sitting in my projects box since then. So it’s about time to try it out. It was not without some problems but I’m real happy with the way it came out. I used a laser to burn the design into copper clad covered in flat black paint. And used a Hydrogen Peroxide(2 parts)/Muriatic Acid(1 part) solution for the etch. It took about 10 minutes with some gentle rubbing to finish the etch and about 2 days to learn Eagle CAD and design a board.
Now off to find those drill bits I bought last year…
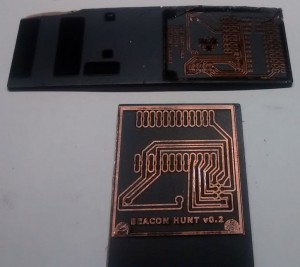
1st Attempt (above) was destroyed with a large guillotine paper cutter. You tube made it look so easy. The 2nd Attempt (below) turned out much better by scoring the copper on both sides and snapping it loose. Also changed the layout with thicker traces just to be sure.
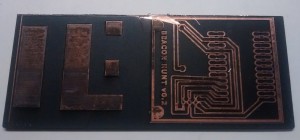
Half the second board was ruined when the razor slipped into the copper on one side. I could probably have masked it off and repainted since this was before the etch, but I wanted to get this thing rolling.
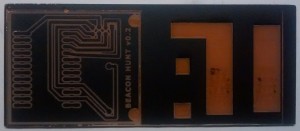
I noticed that areas where the paint was not entirely burned away still etched very well, the paint came off where the laser had heated it but not anywhere else.
ESP8266 WiFi Module Experimentation
I received two WiFi modules today from ElectroDragon.com. These are the newly found and very cheap boards discussed on HackaDay.io. I thought they might work better than the NRF24L01+ modules I’ve been testing for my IoT RaspiBadger side project. Here’s my initial notes to get started:
I’m using the Arduino UNO with this module. The 3.3v/Gnd/Rx/Tx pins of the WiFi Module are directly attached to the same pins on the UNO. I believe I have the Revision 1 (using cmd AT+GMR gives 01000800), the Rev 2 has additional IO pins as well as a reset and ?Enable? pin. Rev 2 will likely not work the way I will describe below for the Rev 1. I tried connecting the WiFi to a pair of AAA batteries at 2.95V and I didn’t get consistent results. I’ll have to explore this further as my end goal is to run this off batteries.
Custom 3d Printer update
Finally got my first large format test print. The calibration tests resulted in replacing the 6mm rod used for driving the x axis belts with an 8mm rod and new pulleys. I had the 6mm rod on hand so I thought I could drill out the 5mm bore pulleys which ended up off center by enough to ruin the x axis movement. I also had to replace the 5mm screws for the idler pulley because the threads were causing binding; I found some 5mm bolts with enough smooth area (grip) to fix this.
I also had to modify the back right panel to make it easier to adjust the x-axis drive belt. It looked nice inset into the extrusions but I couldn’t make any adjustments without disassembling the entire top half of the machine.
After this major revision, I printed off a vase from Thingiverse with a 2 perimeter wall. The layers began to separate after about 40mm getting worse toward the top. Overall, the print seems to be consistent which means the print head movement is good. Once the enclosure is completed I’ll print another vase with the same settings for a comparison with a heated build chamber.
IoT Project
Notes to self on setting up an IoT network using Raspberry Pi as Web and Node servers and Arduino/nRF24L01 modules as clients in a large mesh-type network:
I picked up a couple Nordic nRF24 modules and want to see how they might be used in an IoT capacity. Initial tests with the RF24, NRF24, and RH-NRF libraries went well with modules communicating and LED’s lighting up. That’s all good for the local net but now I need to get the Internet aspect working and that is where all the real work is to be done.
I set up my Raspberry Pi using the project instructions located here. In order to install NodeJS, I had to use the Adafruit instructions located here. So far, so good. This allowed me to control my Arduino via a web page on the local network. Technically this is good enough for a private network controlling a single nRF24 board. But I’d like to have some remote control/feedback over the internet so I can check on the system from afar and interact with multiple devices.
The Instructable located here looks to be a good starting point for incorporating a database to store collected data. But looks to still be on the local network.
Power and Control Panel
Took some time while waiting for the additional extrusions to arrive making a control plate for the I2C panel and power switch. The LCD, SD and encoder are currently being used on my Solidoodle so I’ll switch everything over toward the end. Wow, this is going to look much better than the 3d Printed housing and give me a power switch that the Solidoodle was lacking.
The plate was made from some black on white acrylic from Inventables. The graphics were put together in Corel Draw and cut on my 40W Laser. I put 5mm holes around the edge that will act as a mount and to stabilize the H-frame.
Beginning Work on Custom 3d Printer – Heated Print Bed
Since I’m creating something of my own design, I wanted to go big on the bed to make single prints from large objects instead of assembling from smaller parts. I had quadcopter and OpenRC builds specifically in mind. My Soilidoodle 2 is 6×6 and too small for many things I wanted to print. So this will be a 12×12 plate.
I looked around for some solutions for quick heating. Resistors looked too sketchy for something this big and the Solidoodle takes a long time to heat up with its single resistor. Etched PCBs don’t come this long and I didn’t want to design my own, the cost would be too high anyway. Silicone heat pads looked promising, in fact I have an 8×8 pad from QU-BD that I tested but it took over 10 minutes to heat just a piece of glass and barely attained 90c and had a large variation over the surface. I almost bought a hot plate used for pots and pans but determined that it would be too heavy for a mobile Z-Axis. That left Nichrome as the cheap and easy method. Continue reading
Creating a light from an old scanner.
Sure, LEDs are pretty cheap these days but this light was free. After striping the parts out of an old scanner, I put the lamp in 1/4 inch clear tubing for protection and mounted it with zip ties to some 1″ aluminum angle that I had on hand.
The original board is housed in a custom printed enclosure and runs off 12v. It is a little dim and should probably run off 24v but I don’t have a way to test that right now. I still need to create an extension so the box doesn’t have to be mounted so close to the lamp. I’ll take care of that when it comes time to mount it to the new 3d printer.
Sign for the House
Over the last year I slowly worked on a fancy beach sign for the house. Mostly the vacation and rental homes have them but Ally insisted that we have one too! I spent the most time deciding on the layout. Finally with design in hand, I loaded it into the CNC Router and got started. This also gave me a reason to add endstops for my x/y axis which made aligning the various layers much easier than the eyeballing I had done previously. My kids helped me with the painting, we used an acrylic paint with a couple coats of poly to finish it off.
I’ve had it up for a while now and it still looks good and garners many compliments from many a passersby.